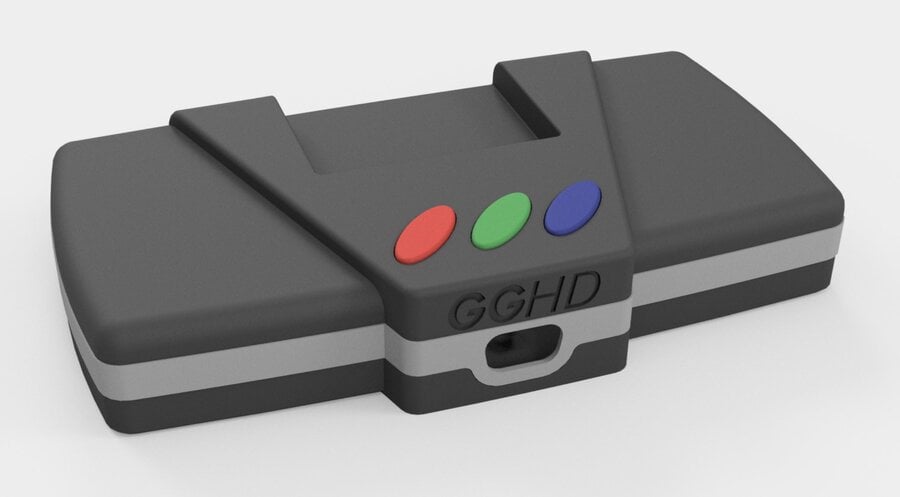
With the recent explosion of retro gaming systems, we're practically drowning in options when it comes to playing vintage games. Clone consoles like the SNES Classic and Mega Drive Mini II offer cheap and cheerful access to some of the best games ever made, while enthusiast platforms like MiSTer require a lot more time and money to get off the ground but can deliver incredible accuracy thanks to the use of FPGA chips.
We now have another option thanks to the efforts of a company called Gamebox Systems, which adopts a slightly different approach to its competitors. We sat down with Gamebox's head of engineering Aaron Silberman (AKA Postman) to talk about the origins of the firm, what it's working on currently and what the future holds.
Time Extension: Could you give us a little background into your company and the people involved?
Aaron Silberman: The formation of Gamebox is a pretty funny story, actually! In the spring of 2018, I (Postman) met Nobble (Elliot) at a gaming convention here in the midwest known as the Midwest Gaming Classic. I went in my Postman cosplay from The Legend of Zelda and knew that some of my heroes from the online forum dedicated to portablisation known as "Bitbuilt" were going to be in attendance at this convention. I walked into the room where all the bitbuilt people were hanging out and immediately recognized all the people in the room... and that's where Nobble and I met. We immediately hit it off, talking about our mods, portables, and project ideas we had that we wanted to make come to life. The best part is we learned we only lived 20 minutes away from each other!
As soon as we got home after the convention, we immediately started hanging out and doing projects together. It started off with one-off projects as I wanted to learn more about coding and hardware engineering, while Nobble was curious about the mechanical design aspects. Once we started making projects that we saw could be more than one-offs, we thought to ourselves, "Hey, we really got something here!". We then founded Gamebox Systems in June of 2019, with our first two products being Cartboy, a Raspberry Pi Zero-based retro emulation handheld kit, and DMTV, a VGA DMG consolizer kit which became the basis for the GBHD consolizer lineup we have today.
Fast forward, and we now have our friend Toad helping us (currently) with the technical documentation and writing. Toad will be moving to Minnesota (where we are based) from Maine this coming spring to work with us and help with day-to-day operations as well as doing his technical writing job. We can't wait to have him!
We also have Dennis Van Den (@PointerFunction on Twitter) on our team doing our mechanical case designs. He is responsible for the GGHD and GBHD Advance SP cases. We look forward to working with him more on upcoming projects!
As of now, it is just Nobble and me physically in the shop. Nobble does the manufacturing of the mechanical cases and ensures all 3D printers are running at maximum capacity while I do research and development, QA testing, customer service, and order fulfilment. Nobble has a second job, and I do Gamebox full-time.
One of your main products is the 'consolization' kits - could you explain how these work and what makes them so special?
The consolization kits were inspired by the original GBA Consolizer by Woozle. We saw how commercially successful it was and thought "let's do that, but let's do it the way we want!" Development started with GBHD Retro (DMG HDMI consolizer) in November of 2019, and our work on developing consolizer kits continues through today, with our most recent consolizer kit being GGHD (Sega Game Gear Consolizer).
Generally, a consolizer is a custom-engineered blend of hardware, mechanical, and firmware engineering to take the video data signals from old consoles and translate those video data signals into something modern HDMI devices can understand and display. This gets paired with a controller (SNES for Nintendo consolizers, Genesis for Sega) and standard USB-C power to create a home-consolized version of the original portable game console. No emulation at all. Only original hardware.
This alone makes it special as it upcycles old, broken, and otherwise antiquated handheld game consoles into something brand new and completely unique. It is the ultimate way to experience your retro handheld gaming consoles. Instead of playing on a screen that is maybe 2 inches large, you can play it on a screen of any size as long as the screen supports HDMI. This is personally good for me as my eyes are not getting any younger!
The video data signals are fed into a chip called an "FPGA" or "Field programmable gate array". This is a specialized type of integrated circuit that is used in this specific use case for real-time image processing. This means that there is only a delay of 3 frames from the original source video image. On top of this, this real-time processing allows us to apply pixel filters/manipulations in real time to the image.
But the uniqueness doesn't stop there. In the firmware of our consolizers, there is an on-screen display (OSD) that can be accessed by holding a button combo for 3 seconds. In that menu, you have the following options:
- 3x display resolutions to choose from (480p, 720p, 1080i)
- 6x scaling options (linear, stretch, TV mode; all with optional overscan)
- 3 unique pixel filter options with adjustable image brightness
- Scanlines/gridlines
- Other small tweaks (RGB LED with animations, change background colour, etc)
Why did you choose to take this approach with old hardware, as opposed to simply retrofitting existing machines with new features?
A large part of it is what I mentioned before, the upcycling of old/broken retro gaming hardware. What we offer is a way to breathe brand new life into these old game consoles and create something that is not only fun to play but is also aesthetically pleasing and pairs well with any gaming setup as a centrepiece.
Gamebox also focuses on and caters to the DIY crowd. Our kits allow people to have a nice weekend project for themselves or perhaps a way to bond with a child and teach them about soldering. While we do offer fully assembled units for our customers that prefer to just have the end product, we also focus equally on the customer that prefers to roll up their sleeves and take on a challenge (or not so much a challenge, depending on skill level). We started off as DIY'ers, and that's who we are to the core. It fulfils the heck out of us to share products that our customers can assemble (or not), knowing that we have our community's back from start to finish.
Another part is the feel of the gaming experience itself. You can, as many people point out to us, emulate these consoles. While that is a good choice for some, it lacks the authenticity that is essential for the hardcore retro gamer. Emulation, while perfectly fine for most, still isn't 100% accurate. It has timing inaccuracies, glitches, game incompatibilities, and sometimes crashes. We, just like our customers, want the best possible gaming experience when we return to play some classic handheld games. There is no better way to experience it than on a Gamebox consolizer.
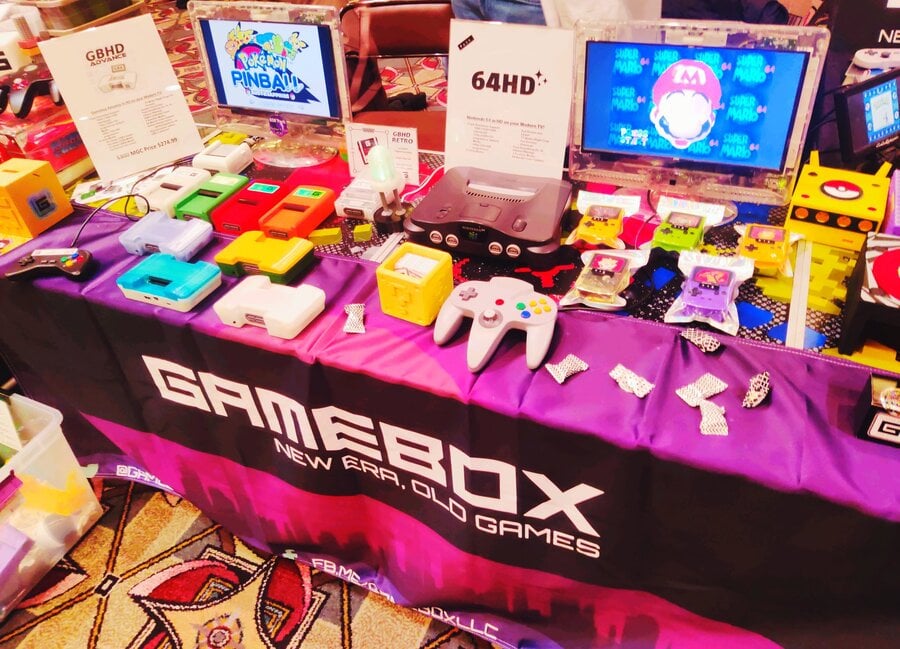
What's been the biggest challenge you've encountered so far?
Definitely has to be scaling 3D printing operations. For those that aren't familiar, the next step up from 3D printing is "injection moulding" which is what you see most all mechanical enclosures in commercial products use. The issue we face is that we are in the midst of mid-scale manufacturing; we cannot justify the cost of injection moulding (Cost can be $10,000 or more for a single mould), but at the same time, we are becoming extremely limited with our 3D printing capabilities. Nobble has been doing an absolutely marvellous job with our manufacturing capabilities, without a doubt. While our capabilities grow week by week, 3D printing has been and continues to be a thorn in our side.
What's the feedback been like from your customers so far?
This can be sorted into two camps, right? The first camp is the camp of people that see the value in our product, the second doesn't and says, "I can just emulate this for the price". So if we only focus on the people that see the value and potentially even make a purchase, the feedback has been overwhelmingly positive.
In the beginning, there were a lot more quality complaints as we were getting our feet planted and sorting out how exactly to put one foot in front of the other when it came to product development and support. Over time, we continued just listening to our customers and implementing their ideas and suggestions and took the criticism to heart.
Currently, feedback has been extremely positive, which makes us elated! We still get criticism, but as always, we listen and internalize the feedback to be better in the future. We will never stop listening to what our customers have to say.
What would you say is the product you're most proud of, and why?
This changes depending on when you ask, but I would have to say GBHD Retro and GBHD Color (both were in the same development cycle). It's not because they are our best products, but it's more about the leap we took from basement modders doing this for fun to an actual legitimate business making commercial products. The products themselves had some flaws since we were just starting out in professional modding, but we did a bang-up job considering it was our first leap.
If I had to answer this from a purely logical (and not nostalgic) standpoint, it would have to be GGHD. No other product like GGHD exists on the market, and it has an absolutely beautiful case design to boot.
What products do you have coming in the future that people should get excited about?
The most buzz we have had about an upcoming product is definitely the Nintendo DS consolizer we are calling DSHD. More details to come in the following months on this project, we are all excited for this product to become a reality!